Durable Solution Against Abrasion in Production Facilities: Pexgol at YPF
Performance evaluation of Pexgol lining under extreme service conditions.
Estudo de Caso Nº
175
Cliente
|
Condições de Trabalho
Solução Pexgol
Aplicação
Comprimento
Categorias
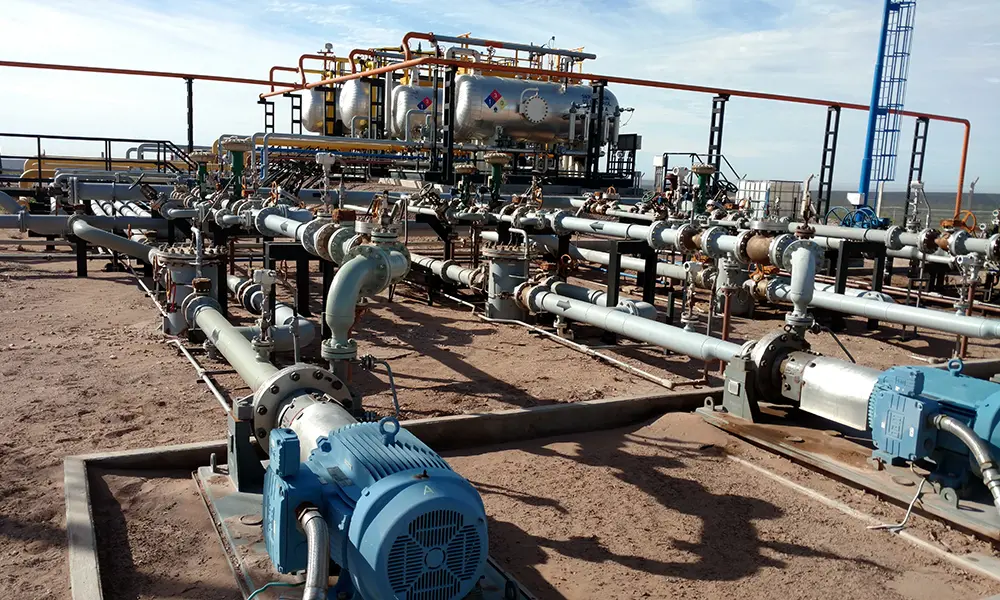
The Challenge
YPF, Argentina’s leading oil and gas exploration and production company, was facing recurring failures in various components of the Aguada Toledo 3 Production Facility (Bat-AT3), particularly in the pump discharge circuit.
The failures were identified in flow restriction areas such as pump discharge reducers, flow control valves, and orifice plates. These components were internally coated with epoxy layers ranging from 250 to 650 µm in thickness.
YPF’s internal studies identified two main deterioration mechanisms:
- Flow-assisted corrosion, considered the most likely cause.
- Localized corrosion due to occluded cells, caused by partial detachment of the internal epoxy lining.
Material loss was estimated at 7 to 9 mm of wall thickness per year under continuous operation, with damage concentrated in reducers and elbows. Considering that the 6” circuit and the 6” to 3” reducing elbow had a wall thickness of 7.11 mm (SCH 40 steel pipe), these failures posed a serious risk to system safety and operational continuity.
The Solution
To mitigate the issue, YPF proposed testing a carbon steel component internally lined with Pexgol to assess its performance under real operating conditions. A 6” x 3” reducing elbow connected to the discharge of one of the pumps was selected for this trial.
The component was manufactured and inspected at Golan’s facility, where the internal Pexgol lining was applied. Once installed and put into operation, the elbow remained in service for 7 years without damage, despite the severe operating conditions.
The implementation of the Pexgol lining proved to be a highly effective solution, eliminating previous failures and significantly extending the system’s service life—without costly maintenance or unplanned shutdowns. This case reinforces Pexgol’s reliability in critical applications where corrosion and abrasion are ongoing challenges.
Estudos de Caso Relacionados
Water Transportation on a Mining Road
|
From carbon steel to Pexgol: A victory against corrosion
|
Pexgol’s Pipe Solution Enhances Salmon Farming
|
New Wastewater Treatment Plant with Pexgol Pipes
|