Overcoming Piping Challenges in Hydrocarbon Transportation
Pexgol’s Piping Solution for Regal Petroleum.
Estudo de Caso Nº
152
Cliente
|
Condições de Trabalho
Solução Pexgol
Aplicação
Comprimento
Categorias
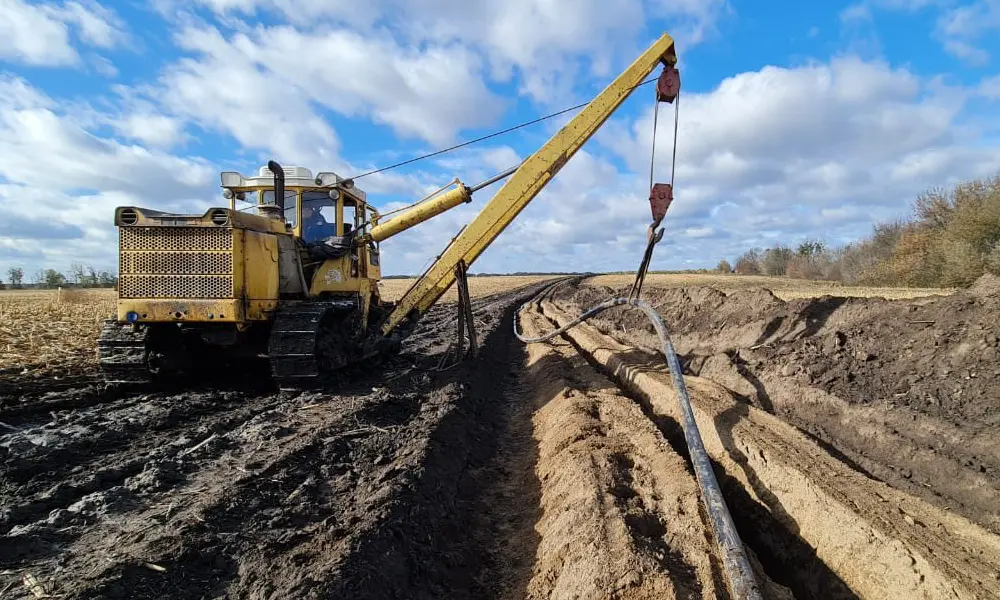
The Challenge
Regal Petroleum Corporation Limited, operating in Ukraine’s Poltava region, faced a significant issue with their existing carbon steel pipeline. Tasked with transporting formation water containing methanol and traces of hydrocarbons, the pipeline suffered from severe corrosion. Additionally, the requirement for underground installation with horizontal directional drilling further complicated the scenario. The project, set in 2023, demanded a durable, corrosion-resistant solution for a pipeline of 110 mm in diameter, stretching over 3,402 meters (11,159 feet) through varied underground conditions. The transportation environment involved a maximum temperature of 15°C (59°F), a fluid flow rate between 4.2 and 8.4 m³/hour, and a pressure of 17 bar. The fluid’s composition was challenging, comprising 20% methanol, less than 1% hydrocarbons and formation water with a pH of 4.4 and high mineralization.
Pexgol Solution
Pexgol presented a comprehensive solution with their PE-X pipes, designed to address the intricate needs of Regal Petroleum.
The installation utilized EF couplers and transition nipples for seamless integration with the existing steel pipeline. Pexgol’s approach emphasized fast installation, lightweight handling, and the efficient transportation of pipes in coils. The initial decoiling process faced hurdles when using a bulldozer, leading to a revised strategy of horizontal uncoiling. A trencher and the Ditch Witch JT3020 drilling equipment facilitated the underground installation, achieving a pullback speed of 0.6 meters per minute.
A key aspect of the project was the customer-specific request for pressure testing:
one 300-meter coil underwent a rigorous test, sustaining a static pressure of 24 bar for 6 hours, validating its suitability for horizontal directional drilling. This demonstrated Pexgol’s ability to meet specialized requirements and underscored their commitment to quality assurance. The successful implementation of Pexgol’s piping system provided a robust, flexible, and corrosion-resistant solution, effectively meeting the complex demands of underground hydrocarbon transportation.
Estudos de Caso Relacionados
Vertical Dewatering
|
Water Transport in Complex Terrain
|