Slurry Lines – Abrasive Dredged Material
Coarse NACL (SALT) Dredging Tailing
Estudo de Caso Nº
1
Cliente
|
Condições de Trabalho
Solução Pexgol
Aplicação
Comprimento
Categorias
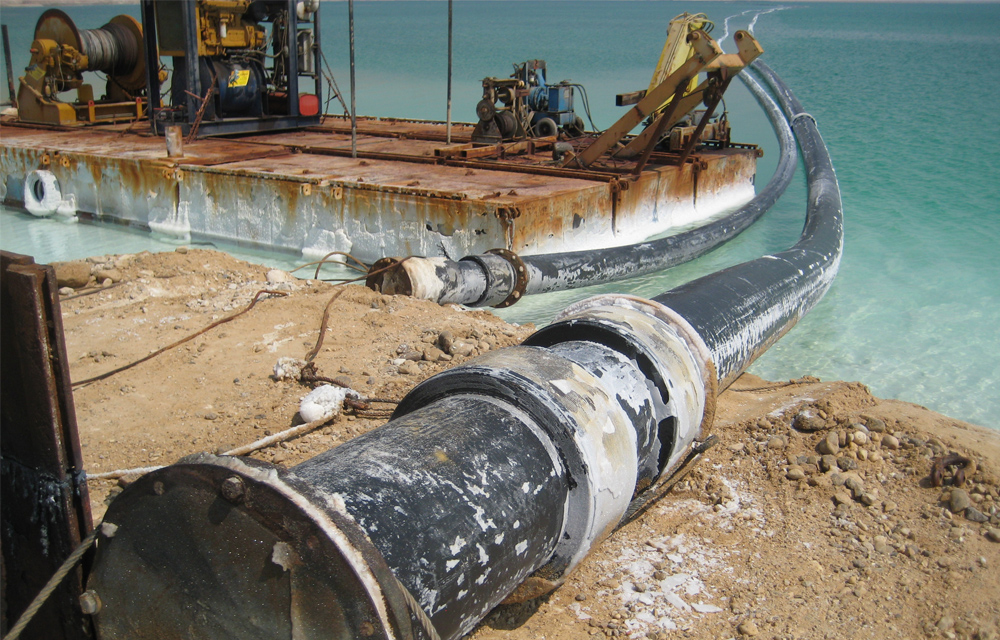
The Challenge
The Dead Sea, located in the Jordan Rift Valley of Israel, is 9.6 times saltier than the ocean, and also known for its high salinity.
The high salinity of brine and the water evaporation creates a constant build-up of salt crystals which requires to be removed. These rough crystal formations are highly abrasive and corrosive. The high temperatures of the area makes material selection more challenging. The salt slurry properties were so harsh that the dredging operators found it necessary to replace their original pipeline every three months due to wear related failures. Before turning to Pexgol, our client tried a number of alternative piping solutions without success:
- Rubber pipes – which proved to be easily damaged by the severe weather conditions and harsh abrasion. This required expensive replacement and maintenance.
- Steel pipes – which were also shown to be easily damaged by the tough climate. In addition, the pipelines weren’t flexible enough, and salt accumulated inside the pipe, causing backup, clogging and low performance.
- HDPE pipes – which did not survive the abrasion of the coarse environment, and as a result, endured a very short lifetime.
Pexgol Solution
Pexgol proved to be the best solution for the client and lasted throughout the first phase of the project without experiencing any failures in the pipeline. The second phase of this project is scheduled for 2017.
By selecting Pexgol, the operator was able to increase his MTBF from 2,500 hours to 43,000 hours (or from three months to 60), which happened to be the remaining lifetime of the project. Without Pexgol, the client would have had to change the entire pipeline almost 20 times during the life of the project.
Estudos de Caso Relacionados
Pulp & Paper Mill
|
Drainage System
|